Use of Compressed Air
Historically, milling operations have used compressed air to provide “motion power” to various systems. Some uses include engaging/disengaging feed rolls, scales, various types of cleaning equipment, and general use for tools and housekeeping. Compressed air systems generally consist of large electric motors to power a mechanical compressor system to provide a positive air pressure that is sent out through a network of piping throughout the mill.
The reality is that compressed air is inefficient and a very expensive way to produce movement. Many studies put the efficiency of a compress air system between 10-15% percent.
There are many factors that contribute to this inefficiency (see chart to right):
- losses due to suction, friction, leaks in the compressor itself (~30% of the energy losses)
- losses for every time the system goes in standby and its restarted (~15%)
- losses generated by the filters, coolers or dryers, (~5%)
- The most common and overseen factor are leaks in valves and hoses, approximately (~10%)
- pressure loss due to valves, bends and the length of the line (~15%)
- losses due to force conversion in the applications itself (~5%)
Other issues include a significant amount of heat and noise generated from compressor operation causing need for ancillary ventilation and use of two forms of hearing protection by our employees. Finally, these systems require significant time and expense for installation and maintenance.
The Maintenance teams have been focusing on identifying and repairing many of the leaks in the distribution system which is saving $1,000’s annually.
Along comes Swisca
Swisca is a vendor based in Switzerland who manufacture a series of equipment focused on improving efficiency and function. Swisca was started by former Buhler employees who sought ways to improve on older, less efficient processes.
One product that Miller has found highly effective are scales (see image to right) that use individual, high-efficiency electric Cervo motors to open and close gate openings. Other competitors’ models of scales performing the same process used compressed air to actuate the slide gates.
Swisca Scales design highlights:
- Straightforward touch screen (much easier to understand for the user than competitor)
- IOT compatible control (IOT Ready to share data with the cloud to improve efficiency)
- High-quality measuring cells (High end load cells to ensure highest precision)
- Energy-efficient servo drives (Biggest difference. 24v servo drives coupled with capacitors will safe over 90% energy compared to compressed air)
- Good accessibility for cleaning (very good sanitation and the whole scale is built out of Stainless)
- Metal detectable connections (all rubber seals are metal detectable)
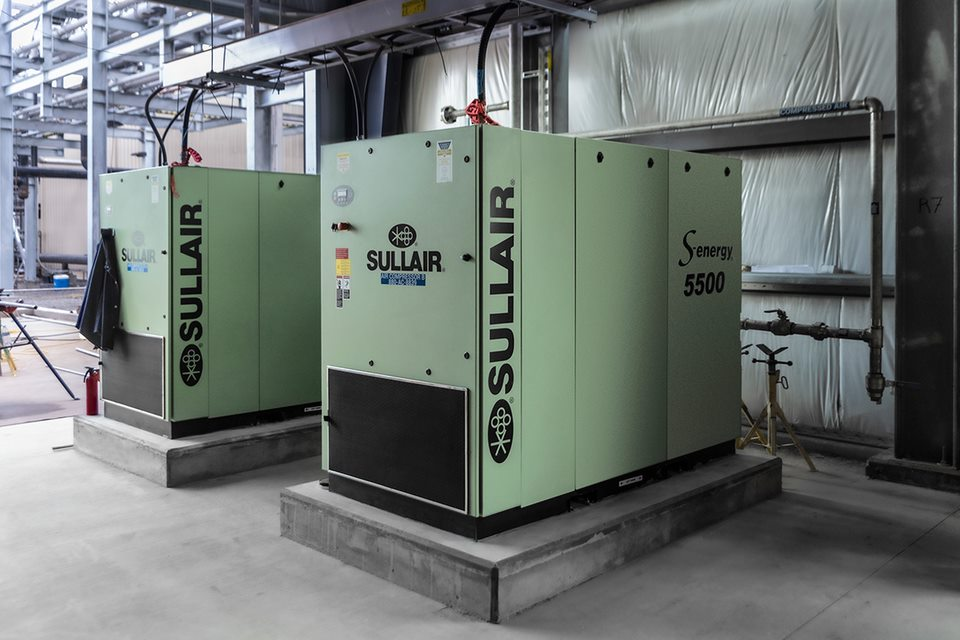
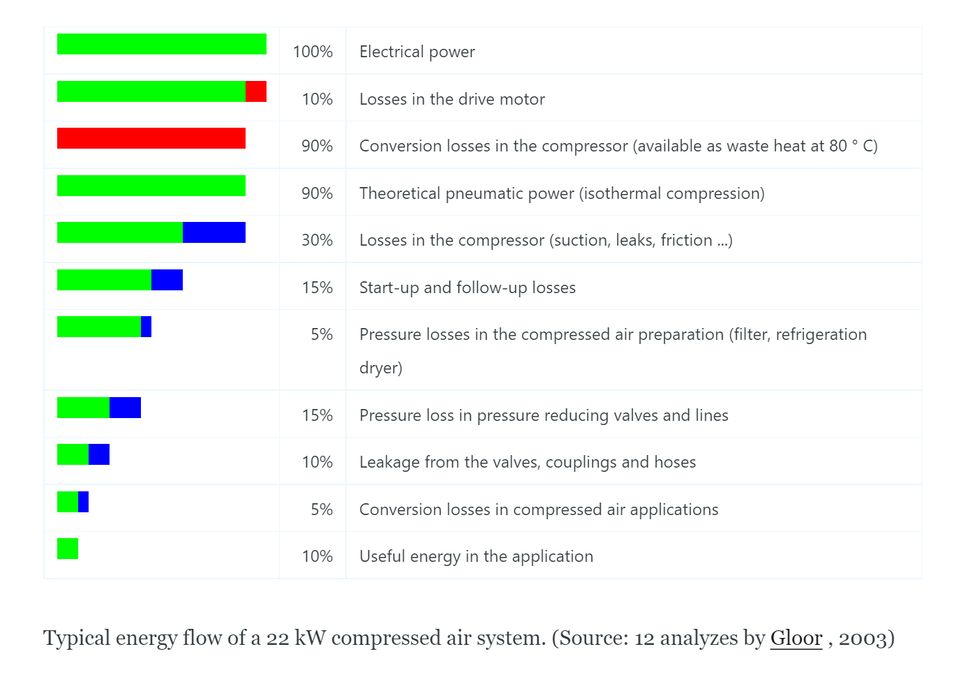
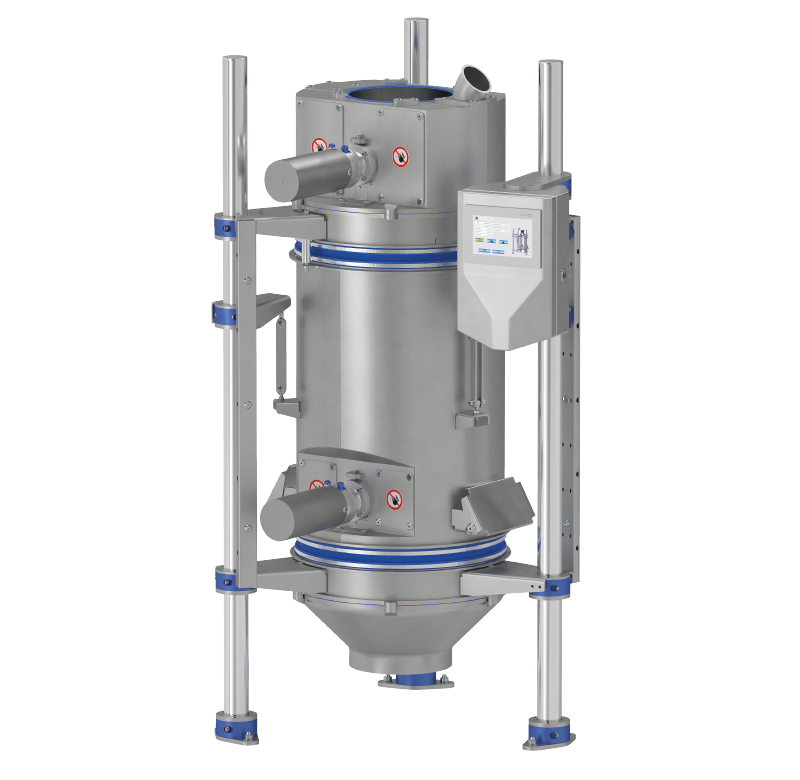
To date, we have installed 53 of the Swisca scales with many more coming as part of other upgrade and expansion projects. These scales are a critical component in the growth of automation and technology we are advancing!
The conservative estimate of the savings by switching from compressed air models to the Swisca Cervo model is ~$70,000 annually.